Energy efficiency is very common in the industry at the moment. On the one hand, the increase in fossil fuel prices has certainly encouraged ecological transition; on the other there is a global commitment to contrast climatic change. From the Paris Agreement and from the Climate Change Conference in Glasgow the goal, which can no longer be postponed, has been to reduce the increasing global temperature to 2° C. Clearly, industry has a frontline role in pursuing this challenge. The sustainable process of industrial decarbonisation involves all business areas, but becomes even more important for those activities with a high energy consumption which results in high CO2 emissions. The ceramic industry is one of them, but technology and innovation can offer interesting energy saving prospects, with positive consequences on both the environment and the competitiveness of the company.
When speaking of energy efficiency, the starting point is to treat the topic by inserting it in a specific context where all the dynamics are considered. Only this way will companies be supported with a solid program made up of suitable investments and tangible results. This is what Progetti has been doing for the ceramic industry for more than 40 years.
“When we talk about energy consultancy,” says Progetti CEO Marco Lora, “we are indicating an energy efficiency service that is the result of careful planning based on real needs, a service that works for the ceramic process and which is developed specifically for the client. We are also convinced that a solution can only be efficient if it has been effectively field tested.”
To this personalised approach Progetti brings the additional value of a deep knowledge of the ceramic sector and its specialisation in MEP plant engineering. Thanks to its deep knowledge the company can assess solutions that optimise consumption without ever endangering product quality, and which in fact increase profit. Thanks to MEP plant knowledge comes the habit of thinking in terms of integrated systems and according to a vision that is naturally guided by environmental sustainability and management.
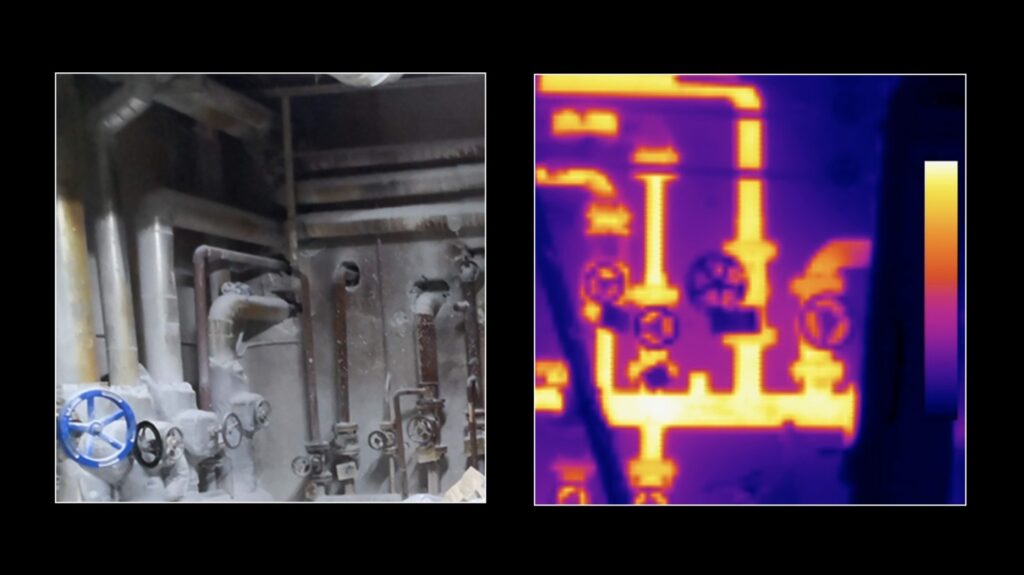
It is well known that the energy requirements of the ceramic industry are very high, with the amounts of thermal energy used being truly immense. The kilns, above all, use lots of energy to reach high temperatures. Recovering heat from chimney stacks is certainly a strategic move. Progetti has developed advanced technical solutions for capturing and storing this energy, which would otherwise be wasted, through direct and indirect recovery systems. The energy is recycled to feed utilities like dryers, supplying dry heat which, when mixed with humid air, satisfies all the setpoints for the best drying process quality. In addition to recycling the energy for the dryers, the purpose of energy consultancy is to analyse the whole energy supply and distribution chain, so as to make it more efficient. Using water as a thermal vector, the thermal energy recovered from the stacks can supply systems for heating, moulding rooms or slips.
The vision should be even wider. To design the best energy scenario, all aspects have to be considered: the MEP services, the different production areas, the structure of the plant. For each aspect, it is important to understand what the saving potentials are.
Progetti’s energy survey follows a well-structured method: it begins with the collection and preliminary analysis of data, crossed with data collected from field visits. At this point an energy efficiency proposal can be formed. The detailed and measurable forecast of the expected benefits gives a precise picture of the return period and, as such, of investment sustainability.
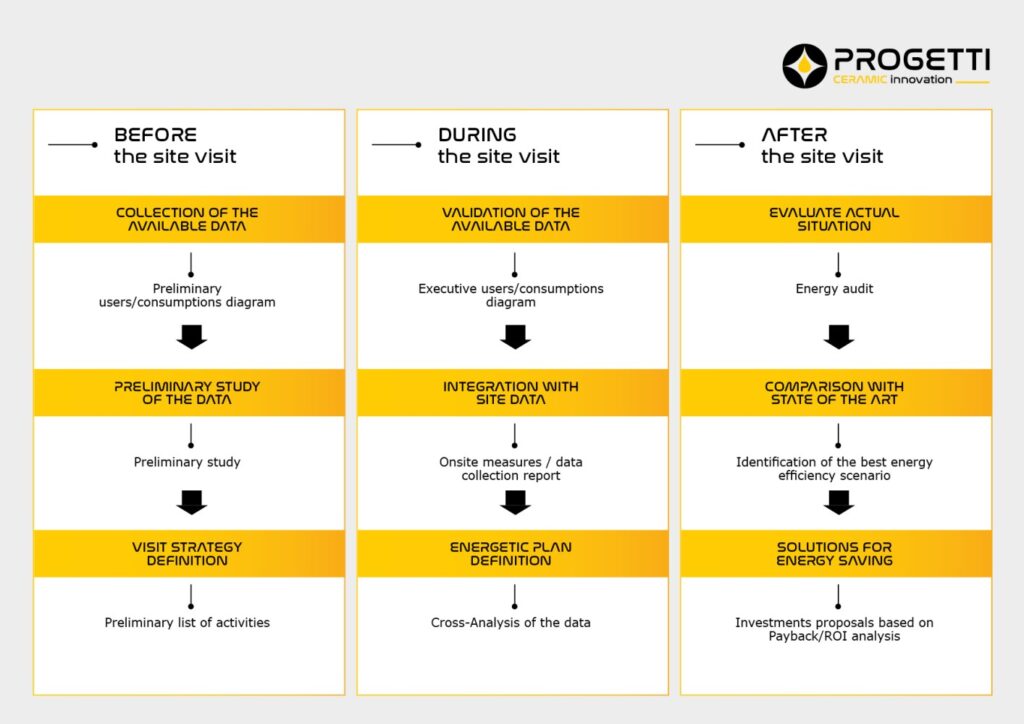
After the energy inspection, client support continues with system engineering and monitoring of the results, which must be in line with what was guaranteed. In this way support can be given globally.
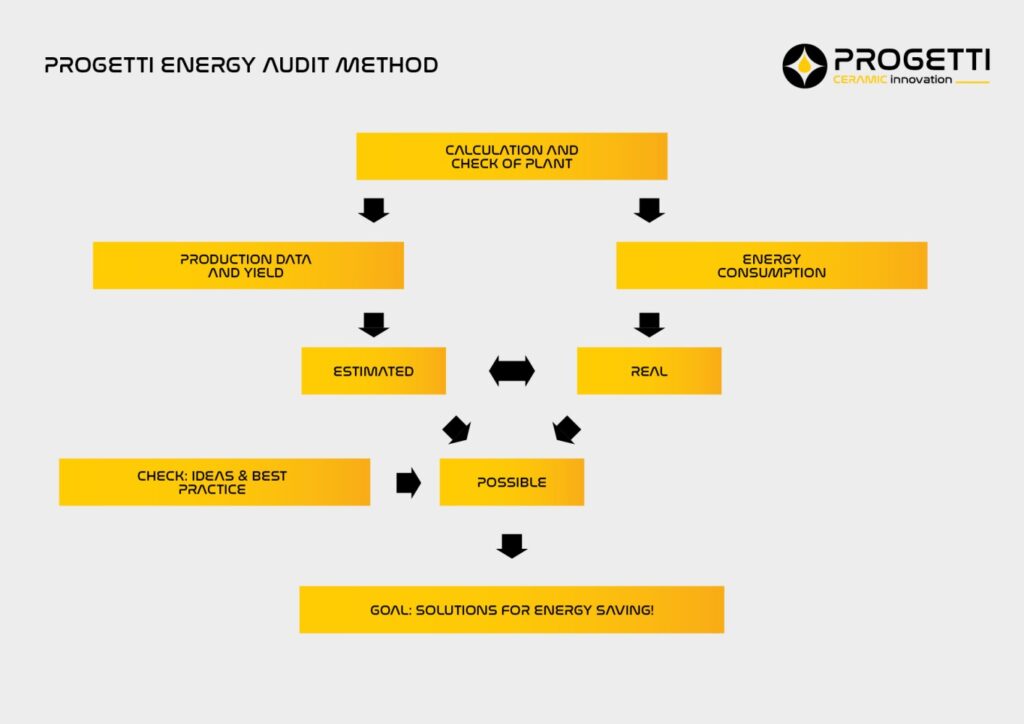