At Progetti, we have always worked to promote the rational use of energy, a commitment with a double goal: to ensure substantial economic savings for our customers and to contribute to reducing the environmental impact of industry production.
Environmental impact reduction is becoming increasingly relevant considering the challenge that ceramic industry is now more than ever called to face. Ceramic industry is in fact notoriously energy consuming.
Another important aspect is the aim at technological innovation, which is also connected to the growing attention to the quality of the working environment and to the achievement of increasingly higher safety standards.
The idea to turn all these challenges into opportunities was at the heart of the project we carried out together with our long-standing customer FV Andina S.A., a leading Ecuadorian company in the production of sanitary ceramics. This way the project has become concretely sustainable.
The project started from a specific requirement: to implement in the production process a continuous dryer, which had to be modern and efficient in terms of productivity and sustainability.
Our engineers, working in close synergy with the company team, were able to exploit energy saving: starting from an all-round assessment of the production process and after an accurate inspection, it was possible to provide the client with a tailor-made continuous dryer working with a zero net energy consumption, a perfect example of sustainable energy engineering.
The company previously used an intermittent dryer, active 365 days a year. In addition, a large area of the plant was dedicated to storing pieces, from 3 to 9 days so that the drying process could finish.
To face the increasing requests from the market and to optimize production costs, the choice was made to implement a technologically advanced system for the drying process. This led to a higher level of competitiveness from a quantity and quality standpoint.
The first step was a study to verify the technical feasibility of a continuous dryer that excluded the use of fuel. The analysis showed that 35,000 m3/h of dry air generated by the tunnel kilns could be recovered to make the dryer work. The heat from flue gas coming out of the stack, reusable through heat exchangers, was also added.
Always with a focus on excellent energy management, we studied the re-introduction of the damp hot air exhausted by the dryer, directing it towards the casting hall to keep the temperature within the ideal parameters.
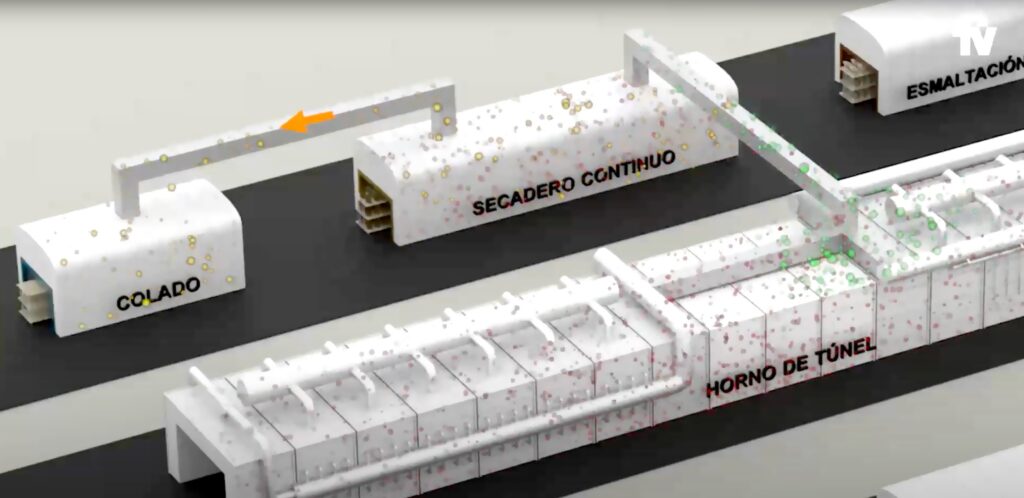
Once in operation, the new dryer confirmed the expected results:
• fossil-free power supply, which equates the annual savings of 60,000 gallons of fuel;
• CO2 reduced by about 630 tonnes per year;
• a considerable reduction in the number of hours that the thermal plant had to work to heat the casting room;
• a decrease in drying times, from days to hours;
• the space previously used for storage was freed, because the pieces come out of the dryer ready for the next step of the production process;
• increased product performance and quality thanks to an optimal parameters control.
Among the advantages of the new dryer, the strong automation should certainly be considered. In fact operators could be relieved from most of the work requiring physical effort.
In addition to feeding the dryer exclusively through recovered heat, solutions have been studied to limit the consumption of the amount of energy required for the electronic control and automation.
“The dryer was built in Italy and then transported to Ecuador, where Progetti supported the customer during the installation and start-up phases,” stated Stefano Striolo, head of Progetti Ceramic Innovation. “One of the main challenges was to perform the system commissioning without interrupting production.”
“We are very satisfied with what has been done and pretty happy of being able to work, as in this case, with customers who have a strong specific competence,” affirmed Marco Lora, the Progetti CEO. “It is very important for us to make our know-how available to them and help them pursue a paradigm of virtuous growth.”